

Unless the vent pipe is unduly long it is normally practical to size it on a maximum flash steam velocity of m/s (30-50 ft sec.). Table 1 gives the recommended minimum vent pipe size for normal conditions but where large volumes of flash steam are being handled by the receiver it may be necessary to increase the vent pipe size to prevent a pressure build up. This can happen where condensate is being handled from traps discharging from high pressure steam in which case some 10 % or more of the condensate may re-evaporate into flash steam.
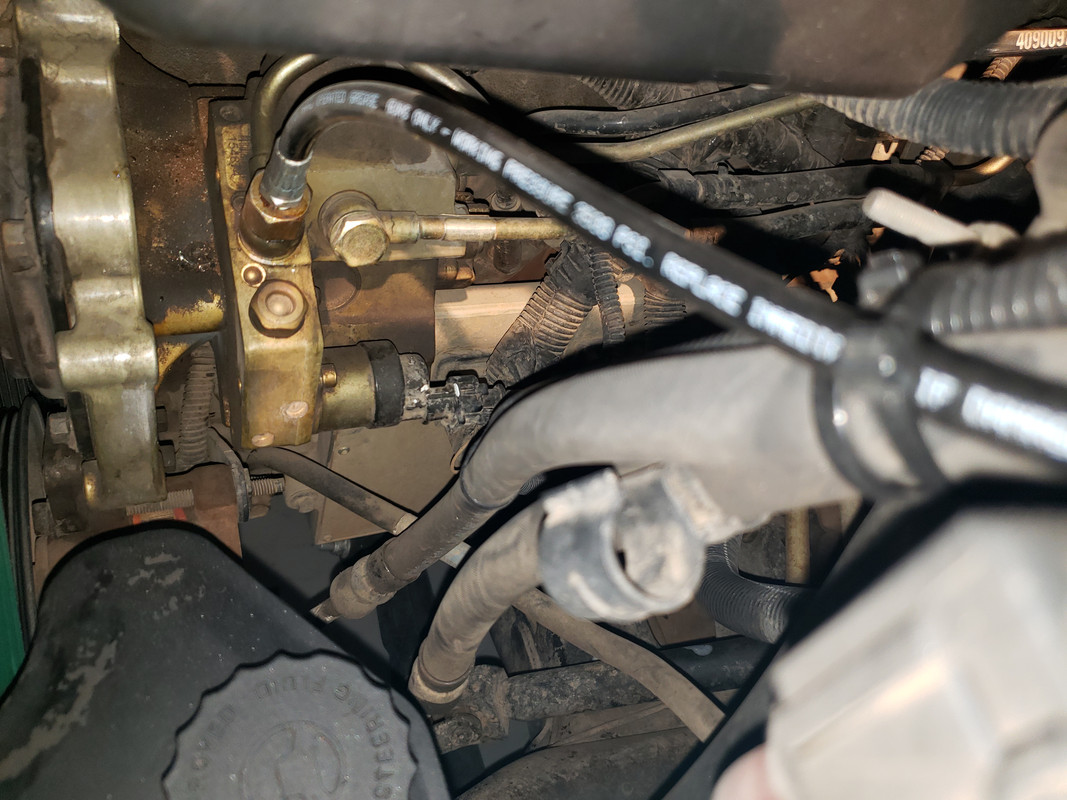
If pressure is allowed to build up in the receiver it will impose an additional back pressure on the traps discharging into the return main and furthermore, it will cause very turbulent conditions inside the pump during the filling stroke resulting in rapid wear.

The vent pipe The receiver should always be fitted with a vent pipe capable of releasing any pressure in the receiver down to atmospheric. Although this dimension of 300 mm (12") is given as the minimum filling head, it is considered to be the ideal and the filling head should not be more than 600 mm (24"). The filling head In order to overcome the frictional resistance of the filling line and to ensure at the same time a reasonable rate of filling, the bottom of the receiver should be not less than 300 mm (12") above the top of the pump. Table 1 gives a guide to the size of receiver necessary. The receiver should have a capacity not less than twice the swept volume (litres per stroke) (galls per stroke) of the pump. After the discharge stroke, with no vented receiver fitted, there would be a turbulent, pressurised flow of this held-up condensate into the pump body, resulting in unnecessary wear of the working parts. If the main condensate return were to be connected direct to the pump inlet, there would be periodic interruptions of the condensate flow from the plant with the very real possibility of intermittent waterlogging and reduced plant efficiency. While the pump is discharging, the check valve on the inlet side is shut so that no condensate can flow into the pump body. The reason for this vented receiver is two-fold. 4, a vented receiver must always be fitted on the filling side of the pump when it is being used for lifting condensate. This arrangement should never be reversed as in Fig The receiver As shown in Fig. In this way any exhaust or vapour which condenses in the pipe will drain back into the receiver. Particular attention is drawn to the fact that the exhaust from the pump is connected into the receiver vent pipe as in Fig. 4 shows the recommended installation layout to ensure satisfactory operation of the pump. 3 shows alternative arrangement when compressed air is used as the operating medium. 2 shows the unit when steam will be used as the operating medium. The pump, receiver and the necessary equipment is mounted in a rigid frame, to save the user time and trouble in setting up the installation. 2) The Spirax Ogden automatic pump is available as a packaged unit. They will then be able to tell you whether the pump is suitable for the revised duty, or whether it can be made suitable by replacement of the valve gear.
#Fass lift pump install instructions serial
If the conditions of operation have changed then it is advisable to contact the manufacturers, Spirax-Sarco Ltd, notifying them of the revised conditions and the pump serial number. Only the check valves supplied with the pump should be used, see Section As despatched each Spirax ogden automatic pump is individually fitted with valve gear most suitable for the conditions of operation stated on the order. They are marked inlet and outlet on the hexagon of the body and have directional arrows cast on the body, and should be fitted accordingly. When despatched these check valves are packed in a separate carton. 1) The Spirax Ogden automatic pump is supplied complete with inlet and outlet check valves. Special applications IM-P Printed in the ST UK Issue 3 Copyright 19981Ģ 1. 1 /3 IM-P ST Issue 3 Spirax Sarco Ogden Automatic Pump Installation and Maintenance Instructions 1.
